©2022 This excerpt taken from the article of the same name which appeared in ASHRAE Journal, vol. 64, no. 1, January 2022.
About the Authors
Michael Gallagher, P.E., is president of Western Allied Corporation in Santa Fe Springs, Calif.
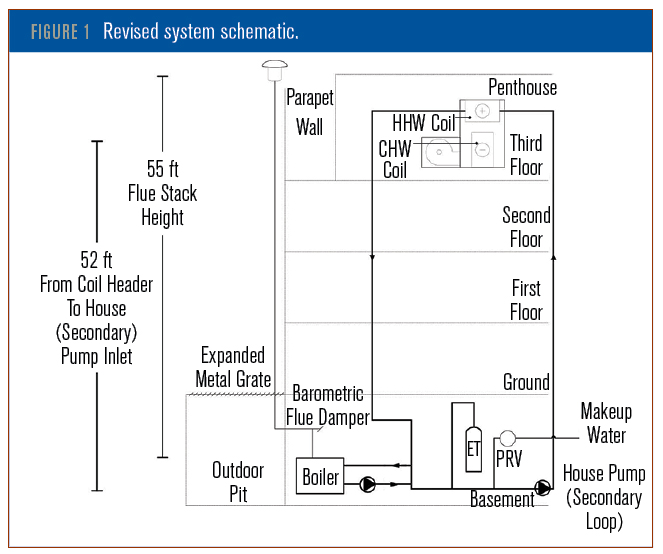
Sometimes the best examples of what not to do come from examples we’ve experienced personally—“war stories.” I have a good example that illustrates several hydronics points. Please glance first at Figure 1 to orient yourself to the system being discussed, then refer to it as you read.
A few years ago I picked up service responsibility for a three-story building with chilled water and hot water loops serving a dual duct VAV system. The air-handling units (AHUs) were located in a rooftop penthouse. The chillers were also on the roof, but the boiler was in the basement.
Within a few months of our arrival at the building, the heat exchanger in this copper tube boiler sprang a leak. The damage was extensive: the refractory was ruined, the burners were cracked, the circuit boards got wet. Even though the boiler was only nine years old, the owner decided to replace rather than rebuild this standard, non-condensing boiler. I then went to look more closely at the situation.
The immediately obvious issue was that the boiler’s little primary circulating pump was piped in series with the house pump. There was no decoupling pipe between primary and secondary loops; as a result, there were no primary and secondary loops; it was all a primary loop with two pumps in series (Figure 2). “That will be easy to fix when the boiler is replaced,” I thought.
The proposal generation process moved ahead, and it occurred to me that the vent stack (boiler flue) was pretty high. I knew it ran from the basement up along the side of the building and extended above the roof, and I had not noticed anything other than a simple flue. On another jobsite trip I confirmed the flue was approximately 55 ft (16.8 m) in vertical height.
This poses a problem (although an easy solution exists); this particular boiler manufacturer’s literature states that vent stack height should be 25 ft (7.6 m) or less. Above that, a concern exists that the uplift force of the draft will become too great and draw too much combustion air through the unit. This excess air can have several negative effects, including lower efficiency (too much heat ends up going up the flue, as opposed to transferring to the water in the tubes); a short, oxidizing flame that can increase burner corrosion; too much air through the combustion fan, which can overload the motor, etc.
The solution is to add a barometric damper in the flue at the boiler, adjusted so that beyond a particular draft pressure, the barometric damper will open to permit room air to rise through the vent stack instead of having the vent stack draw excess air through the combustion system.
Fast-forward several weeks, and the boiler replacement occurred. The piping and flue were revised as described (Figure 1). The boiler started and everything was fine. However, nobody inspected the air-handling units on the roof. The next day we were called back to the building. The boiler appeared to be working fine, but there was no heat at the AHUs. One of our techs stopped by and found that, sure enough, we were making 160°F (71°C) water in the basement in the little boiler primary loop, but the supply water leaving the basement in the secondary loop was about 110°F (43°C), and the return was colder than that. We found that there was air in the piping at the AHUs.
A good field tech will look further than that, once the situation is recognized. He found that the automatic air vents were gummed up, and the building staff said they would replace them. The tech also suspected that the partial drain down that had occurred during the boiler replacement may have loosened some crud in the piping loop, and that the strainers upstream of the AHUs’ heating water control valves might have been plugged. The owner’s staff agreed to check that.
Read the Full Article
ASHRAE Members have free access to the full-text PDF of this article as well as the complete ASHRAE Journal archives back to 1997 in the Free Member Access Area.
Non-members can purchase features from the ASHRAE Bookstore. Or, Join ASHRAE!
Return to Featured Article Excerpts
Return to ASHRAE Journal Featured Article Excerpts